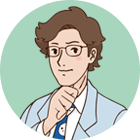
近年、製造業のキーワードとなっている「スマートファクトリー」。デジタル技術を活用し、生産ラインや装置のデータを収集することで、効率的かつ安定した生産を目指す工場のことです。しかしデータ収集と聞いて、何から始めればよいか分からない・装置設計の変更が不安という方も多いかもしれません。今回は、スマートファクトリー化の最初のステップとして開発されたACサードライブによる、データ収集・活用の方法をご紹介します。
そもそも生産ライン・装置のデータを収集する目的・方法とは?
スマートファクトリーにおけるデータ収集の目的は、そのデータを活用し、より効率的かつ高品質で安定した生産活動を行うことです。生産ラインやラインを構成する装置のデータをリアルタイムに収集、解析し、その結果をフィードバックすることで、生産活動を改善していきます。
様々な分野でこのスマートファクトリー化の流れが加速する中、「自社の工場もスマートファクトリー化したいが、どこから着手したらいいのか分からない」という方もいらっしゃるのではないでしょうか。
スマートファクトリー化の一般的なステップは、以下の3段階です。
①データ収集・見える化
②分析・解析
③データによる制御や最適化
安川電機ではこのステップのうち、①生産ラインや装置の中にあるデータ収集・見える化、②分析・解析を実現できるACサーボドライブ「Σ-Ⅹ(シグマ・テン)」を開発しました。
生産ラインやラインを構成する装置の中には、スマートファクトリー化に必要な“価値のあるデータ”がそろっています。この価値のあるデータをΣ-Ⅹによって収集・分析することで、例えばラインの突発的な停止や故障を予防でき、安定した生産が可能になります。
次章からはΣ-Ⅹによるデータ収集・活用のステップと、Σ-Ⅹを使用するメリットを紹介しましょう。
ステップ①サーボモータで、各種データをリアルタイムに収集
ACサーボモータΣ-Ⅹは、サーボ単体のセンシング機能により、装置にセンサーを追加することなく、データ収集が可能になります。またΣ-LINK IIセンサネットワークとの組み合わせにより、各種センサー情報も時間軸を合わせて収集解析することができます。
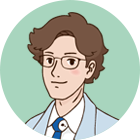
Σ-LINK IIとは?
サーボと各種センサーの情報を一本化して収集するネットワークです。サーボパックとサーボモータのエンコーダ間通信の高機能・高信頼性通信を維持したまま、センサーやI/O機器のカスケード接続が可能です。
サーボモータがセンサーとなり、装置設計不要で各種データを収集
Σ-Xは、サーボモータをセンサーとして活用することで、サーボの設置環境の情報やサーボの使用部品の寿命をセンシングし、その結果をモニタリングします。例えば、サーボモータのベアリングやオイルシールのセンシング結果を基に、モータのメンテナンス予測をモニタリングできます。これにより、メンテナンス時期の的確な判断と、突発的な故障の防止に役立てられます。
また、サーボモータをセンサーとして使用できるため、装置内にセンサーを追加する必要ありません。装置の設計変更をすることなく、すぐにデータ収集を始めることができます。
Σ-LINK IIを活用して、モータとセンサーの時間軸のあったデータを収集
サーボ単体でもデータ収集は可能ですが、さらにΣ-LINK IIセンサーネットワークを活用して、各種センサー情報を同時に収集することもできます。Σ-LINK IIインターフェイスを搭載した「Σ-LINK IIセンサハブ」は、様々な市販のセンサーを複数接続できるのが特長です。これらのセンサー情報は、Σ-Ⅹサーボモータが収集するデータと時間軸のあった状態で収集されます。サーボ周期(μs)と同期した質の高いデータを収集できるため、データ処理の工数を削減することができます。
Σ-LINK IIの活用で、装置内装機器レイアウトの最適化と省配線化
Σ-LINK IIを活用する場合、センサハブをモータとセンサーに近い部分に設置することで、省配線化を実現できます。また、センサーからコントローラまでの配線を短くできるため、ノイズなどの影響を避けられます。
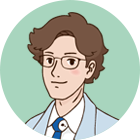
Σ-Ⅹはサーボ単体のセンシング機能が強化され、さらにΣ-LINK IIと組み合わせることで、各種センサー情報も時間軸を合わせて収集解析できるようになりました。
装置設計を維持したまま、すぐにデータ収集を始めたい場合はΣ-Ⅹ単体を使用する。データ収集をさらに強化し、今まで以上に装置を高性能化・高機能化したい場合にはΣ-LINK IIを活用する、という段階的な使い方もできそうですね。
ステップ②収集したデータをサーボで解析し、装置の異常を検知
ファーストステップのデータ収集が実現できたら、次は収集したデータの活用です。Σ-Ⅹは、収集したデータの活用までサーボ単体で完結できるのが特長です。ここからは、データ活用の例を見ていきましょう。
稼働データの数値化から異常検出まで、収集データの活用もサーボ単体で完結
Σ-Ⅹは、サーボが収集した様々なデータを基に、サーボ自身が解析しフィードバックします。例えば、装置の振動・外乱・トルク指令などのデータから傾向を予測することで、突発的な停止や故障の予防につながります。
もちろん、Σ-LINK IIを使用して収集したセンサーデータも、サーボが解析し活用できます。
データ活用により、装置の“いつもと違う”を検知
Σ-Ⅹには、異常検知機能や振動情報モニタ、回生過負荷余裕度など様々なセンシング機能や動作最適化モニタのデータ活用機能があります。ここでは、代表して異常検知機能の仕組みをご紹介します。
異常検知機能とは、サーボが装置の振動変化を監視することで装置の異常を検知できる機能です。異常検知機能では、装置の運転の前に、あらかじめサーボパック内に動作の標本データを保存します。同じ動作パターンで運転させ、標本データと実際の運転データを比較することで、異常を検知します。
この異常検知機能により装置の変化を捉え、経年劣化による装置異常の検出、生産品の良否判断、組立精度の確認などに役立てることができます。
Σ-Ⅹによるデータ収集・データ活用を始めるには?
Σ-Ⅹは、スマートファクトリーの実現に向けた、重要な最初のステップを支えるサーボドライブです。データ収集を始めたいが方法が分からない、収集したデータで何ができるか悩んでいるといった疑問をお持ちの方は、まずはお問い合わせページからぜひお気軽にご相談ください。
次回の豆大福先生は、Σ-Ⅹの「装置性能を最大限に引き出すモーション性能編」をお届けします。ご期待ください!
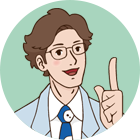
解説のポイント
- 安川電機では、スマートファクトリー化に必要な「データ収集・見える化」「分析・解析」を実現するACサーボドライブΣ-Ⅹを開発。
- Σ-Ⅹはサーボ単体で、装置のリアルタイムなデータ収集が可能。Σ-LINK IIネットワークと組み合わせ、複数のセンサーデータの同時収集もできる。
- 収集したデータをサーボ自身が解析し、装置の異常検知など様々なソリューションをサーボ単体で完結できる。