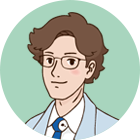
機械設備の故障による生産ラインの突発的な停止は、生産性の低下やコスト増などの多大な損害を引き起こします。そうした状況を防ぎ、最小限に抑えるためには、異常検知による予防保全や、迅速な復旧のための原因究明の仕組みが必要です。今回はこの仕組みづくりを簡略化し、装置の付加価値向上をサポートするツールをご紹介します。
生産停止の損害を最小限に…予防保全が主流 仕組みづくりに課題も
機械・設備の故障によって、生産ラインが突発的に停止してしまうと、「製品を作れない」うえに、以下が発生します。
例えば……
・生産数低下をカバーするための人員確保、人件費アップ
・故障原因追及のための調査コスト発生
・特急修理のためのメンテナンスコスト発生
・ユーザーからの注文に対応できず、機会損失・信頼低下
もし故障の原因分析や交換部品の調達に時間がかかれば、それだけ損害も大きくなります。
損害を最小限に抑えるため、現在製造業の世界では「予防保全」の考え方が主流になっています。予防保全とは、機械・設備が壊れる前にメンテナンスを行うという考え方です。例えば、普段から装置の稼働データを取得しておくことで故障の予兆を把握し、前もって保全計画の立案や交換部品の調達を行います。いざ装置が止まっても、生産停止の時間を最小限に抑えられます。
「定期メンテナンスを行っているから、予防保全の仕組みづくりはまだ必要ない」と感じられる場合もあるかもしれません。しかし、定期メンテナンスを行っていても、機械・設備によっては見つからない場合や人の目では分からない部分があり、異常を見逃してしまう恐れもあります。
また、予防保全に加えて、復旧までの時間を最小化することも重要です。故障原因を迅速に調査・究明できる仕組みも作っておく必要があります。しかし、こうした仕組みづくり自体に、どこからどう着手していいか分からない・取り組む時間が取れないといった課題があります。
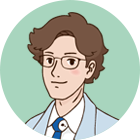
近年、製造業のキーワードとなっている「スマートファクトリー」は、機械・設備のデータを収集することで効率的かつ安定した生産を目指す工場のこと。こうした工場では、収集したデータを予防保全に役立てる仕組みができているといえます。
予防保全&原因究明の仕組みづくりを簡単に!アプリケーションパッケージとは?
生産現場のこうした課題に対して、安川電機では、予防保全やモーション制御の仕組みづくりをサポートする「アプリケーションパッケージ」というサービスを提供しています。
今回は、アプリケーションパッケージで提供しているプログラムのうち、「異常検知」と「YCPドライブレコーダー機能」を使用することで、予防保全と故障の原因究明を効率化する仕組みづくりの方法をご紹介します。
アプリケーションパッケージとは?
アプリケーションパッケージは、MP3000シリーズコントローラで使用するプログラムです。お客様のコントローラアプリケーションプログラムに適用することで、プログラム作成の簡略化や装置の付加価値向上を目的としています。
具体的には、機能ごとに提供されるプロジェクトファイル(.YMW7)やアドオンアプリなどを、MPコントローラのエンジニアリングツール「MPE720 Ver.7」やパソコンに適用して使用します。
予防保全の仕組みづくり「異常検知」で、“いつもと違う”に気づく
アプリケーションパッケージの「異常検知」機能は、MPコントローラで機械・設備の“いつもと違う”を検知し、予防保全に役立つ機能です。MPコントローラに集まる様々な機器のデータを利用し、異常検知を行います。
この異常検知機能は、監視対象(検知したい機器)の標本データと直近の動作データを取得し、それらを比較することで異常度を算出するという仕組みです。異常度の上昇具合を把握しておけば、故障する前に部品を交換でき、生産ライン停止の時間を最小限に抑えられます。
通常、異常検知を行うには、機器それぞれに検知のしきい値を設定し、いちからプログラムを作る必要があります。このアプリケーションパッケージで提供されるサンプルプログラムを使用することで、プログラム作りを簡略化できます。また、検知専用の機器も不要で、既存設備で異常検知を始められます。
サーボパックで行う異常検知とは何が違う?
安川電機のサーボパック(Σ-Ⅹ)にも異常検知機能が備わっていますが、コントローラで行う異常検知とは特徴が異なります。
取得するデータの細かさ(精度)の点ではサーボの方が有利ですが、コントローラはサーボ以外の様々な機器データも取得できるため、異常検知の材料が幅広いというメリットがあります。
・サーボとコントローラの異常検知の対象の違い
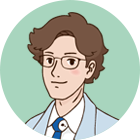
故障、そして生産ライン停止の“前”の備えとして、異常検知の仕組みを作っておいてはいかがでしょうか?
原因究明の仕組みづくり「YCPドライブレコーダー機能」で、“何が起きたか”を知る
「YCP∗ドライブレコーダー機能」は、故障などにより生産ラインが停止した後の速やかな原因究明に役立つ機能です。YCPドライブレコーダー機能とは、故障や異常が発生した際、コントローラのロギングデータと画像情報を同期させて、原因を解析できる環境を提供するものです。
∗YCP:YASKAWA Cockpitの略。工場の設備や装置をつなげることで、生産現場や装置のデータをリアルタイムで収集・蓄積・分析できるソフトウェア。パソコンにインストールして使用します。
車のドライブレコーダーのように、故障の直前・直後で何が起きていたかをすぐに確認・分析できるため、原因調査の時間短縮に貢献します。あらかじめアラームなどのイベント(トリガー)を指定しておき、発生時に検証したり、原因が掴みづらい機構や動きが分かりづらい部分などをクローズアップして撮影したりすることもできます。
YCPドライブレコーダー機能は、既存設備にYCPとカメラを追加することで実装できます。
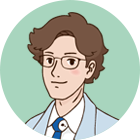
「異常検知」が故障の“前”の備えならば、「YCPドライブレコーダー機能」は故障の“後”の備えとなるものです。2つをセットで使うことで、生産ライン停止による損害対策を効率的に行うことができます。
アプリケーションパッケージを活用し、突発的な生産ライン停止に備えませんか?
アプリケーションパッケージの「異常検知」と「YCPドライブレコーダー機能」を活用することで、予防保全と故障の原因究明の仕組みづくりを簡略化でき、生産ライン停止や復旧にかかる時間の最小化につながります。
アプリケーションパッケージを使った仕組みづくりに少しでも興味を持たれたら、まずは一度お問い合わせください。以下のページでは、各機能のシステム構成や動作概要などをまとめたガイダンス資料をご覧いただけます。(※会員サービス)
▶アプリケーションパッケージのガイダンス資料を見る(システム構成・動作概要など)
▶お問い合わせはこちらのメールアドレスへ:mech-lib@yaskawa.co.jp
※後日、担当者よりご連絡いたします。
また、今回ご紹介した2つの機能のほか、モーション制御の「制振位置決め制御」も用意しています。こちらも詳細はお気軽にお問い合わせください。
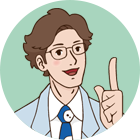
解説のポイント
- 故障による生産ラインの停止は生産性の低下やコスト増などの多大な損害を引き起こす。損害を最小限にするため、予防保全の考え方が主流に。
- 安川電機では、マシンコントローラを使用した予防保全や故障の原因究明の仕組みづくりに役立つ「アプリケーションパッケージ」を提供している。
- アプリケーションパッケージの「異常検知」は機械設備の“いつもと違う”を検知し、「YCPドライブレコーダー機能」は故障の原因調査を効率化できる。